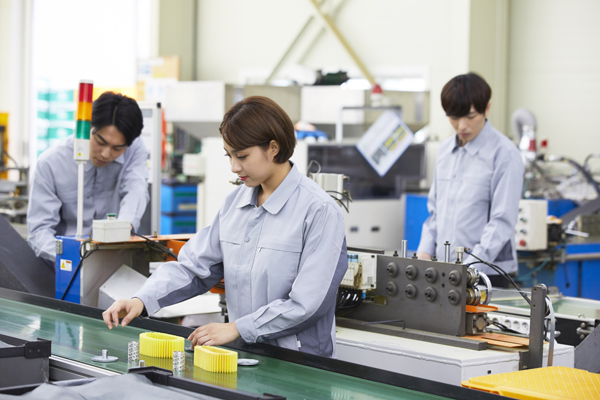
部品・資材のカウント作業、多発するヒューマンエラーが生産性を下げる正確で効率的な「棚卸」を実現した“マルチな”先進技術とは?
組立加工メーカーF社 製造部
家電から車載製品まで、幅広い電子機器類の組み立て加工を請け負うF社。棚卸は半期ごとに行っていたが、半製品の在庫は把握できていても部品や資材については正確な数値の把握が難しく、そこで発生する棚卸誤差が毎回、問題視されていた
課題
部品・資材の棚卸作業で、人の手によるカウントによってミスが発生している
F社の現場で特に難しい課題となっているのは、小さな金属部品や電子デバイス類の数量を正確に把握することでした。
現状、専用容器やレールなどを使ってカウントを行っていましたが、人の手による作業のため、対応する作業員によってはミスや漏れが度々発生。結局、この作業を熟練工だけに任せることになり、多大な負担や時間がかかっている状況でした。また、見た目はほとんど同じでディテールや素材がほんの少し違う、枝番違いの紛らわしい部品なども多く、これらは誤品カウントの温床となっていました。そして現場では、こうしたカウントの間違いによる欠品が原因で、生産がストップしてしまう事態が年に数回は起こっていたのです。
一方、資材に関しても、特に液体・粉体の種類や使いかけ残量を判別し把握するのに苦慮していました。というのも、取り扱う多種の資材の中には似たような容器、キャップが複数存在し、目視での正確なカウントには限度があったのです。当然、カウント間違いが少なからず発生し、スムーズな製造に影響を及ぼしてしまうことがありました。
バーコード、ICタグによるカウント方法は多様な形状を持つ全ての対象に適用できない
製造部を仕切るM氏は、厳密な正確性が求められる棚卸について、ヒューマンエラーのリスクを避けてもっと効率化できる方法がないかと思案し始めました。バーコードやICタグの導入を考えましたが、形状や種類の多さから、取り扱うすべての部品・資材のカウントに適しているとは言えないと判断し、一旦断念せざるを得ませんでした。